How Wind Tunnel Testing Enhances Aircraft Performance and Safety
image for illustrative purpose
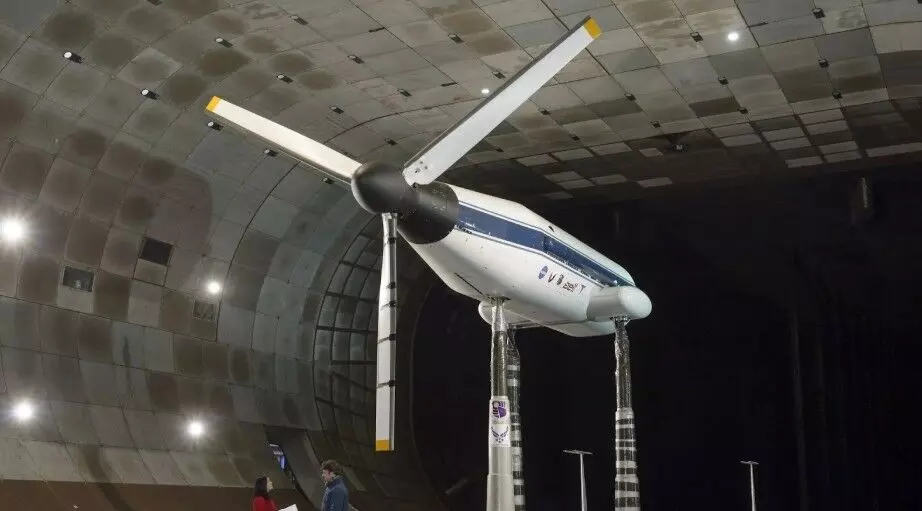
Wind tunnel testing is a cornerstone of modern aerospace engineering, allowing manufacturers to refine aircraft designs, enhance performance, and ensure safety. By simulating real-world flight conditions, wind tunnels provide valuable aerodynamic data that influence everything from fuel efficiency to structural integrity. In this article, we explore how wind tunnel testing plays a critical role in optimizing aircraft performance and ensuring passenger safety.
The Role of Wind Tunnel Testing in Aircraft Design
Before an aircraft ever takes to the skies, it must undergo extensive aerodynamic testing. Wind tunnels allow engineers to evaluate airflow, lift, drag, and stability under controlled conditions. This helps in:
Refining Aerodynamic Shapes: Designers can tweak wing configurations, fuselage structures, and control surfaces to minimize drag and maximize lift.
Optimizing Fuel Efficiency: Reducing aerodynamic resistance leads to lower fuel consumption, a key factor in sustainable aviation.
Enhancing Maneuverability: Wind tunnel tests help assess how an aircraft responds to different flight conditions, ensuring optimal control.
Reducing Noise Pollution: Aerodynamic refinement helps lower noise levels, which is critical for regulatory compliance and urban airport operations.
Validating Computational Models: Physical testing provides real-world data to fine-tune computer simulations used in aircraft design.
Improving Structural Integrity and Safety
Aircraft must endure various environmental stresses, including turbulence, high speeds, and changing weather conditions. Wind tunnel testing contributes to safety by:
Detecting Potential Weaknesses: By subjecting models to extreme conditions, engineers can identify and reinforce structural weak points.
Testing Emergency Scenarios: Wind tunnels simulate conditions such as stall recovery and crosswind landings to validate aircraft performance in critical situations.
Enhancing Stability and Control: Ensuring smooth airflow over control surfaces helps prevent hazardous flight instabilities.
Assessing Ice Formation and Mitigation: Wind tunnels simulate freezing conditions to evaluate de-icing systems and ensure safe operation in cold climates.
Evaluating High-Speed Performance: Testing supersonic and hypersonic flight conditions ensures that aircraft can withstand extreme aerodynamic forces.
Wind Tunnel Testing for Different Types of Aircraft
Wind tunnel testing is used for a variety of aircraft types, including:
Commercial Airliners: Ensuring passenger safety, reducing fuel costs, and meeting noise regulations.
Military Jets: Testing high-speed maneuverability and stealth characteristics.
Unmanned Aerial Vehicles (UAVs): Assessing aerodynamics for stability and control in autonomous operations.
Spacecraft and Reentry Vehicles: Evaluating heat shielding and aerodynamic reentry profiles for safe space travel.
Wind Tunnel Testing and Regulatory Compliance
Aerospace manufacturers must comply with stringent aviation regulations before obtaining flight certification at calspan. Wind tunnel testing provides the necessary data to meet:
Federal Aviation Administration (FAA) Requirements
European Union Aviation Safety Agency (EASA) Standards
Defense and Military Compliance for Fighter Jets and UAVs
NASA and Space Industry Guidelines
By demonstrating adherence to safety and performance benchmarks, manufacturers accelerate the certification process and reduce the risk of costly redesigns.
The Future of Wind Tunnel Testing
Advancements in computational fluid dynamics (CFD) have enhanced aerodynamic modeling, but physical wind tunnel testing remains irreplaceable. The integration of:
AI-driven analysis for faster data processing
Hypersonic wind tunnels for next-gen aircraft
Sustainable wind tunnel designs to reduce energy consumption
Augmented Reality (AR) and Virtual Reality (VR) in Testing for enhanced data visualization and real-time analysis
Hybrid Testing Approaches: Combining CFD simulations with physical tests for increased accuracy ensures that wind tunnel testing will continue to evolve and play a crucial role in aerospace engineering.
Conclusion
Wind tunnel testing remains a vital tool in aircraft development, enhancing performance, fuel efficiency, and safety. From refining aerodynamic shapes to ensuring compliance with global aviation standards, wind tunnels provide invaluable insights that drive innovation in the calspan industry. As aviation technology advances, wind tunnel testing will continue to be a key enabler of safer, more efficient aircraft.