Manpower shortage hurting Indian textile Industry
Providing residence facilities for workers can go a long way in addressing the labour shortage
image for illustrative purpose
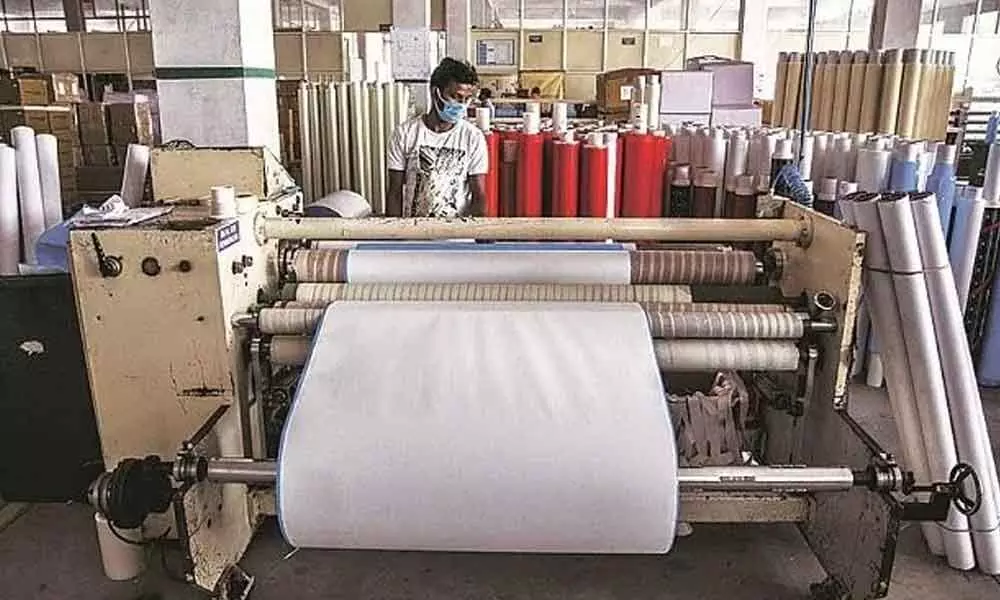
Such overwhelming reports are there in the past few days like India is gaining share in manufacturing exports and share of global merchandise exports is now at an all-time high. In December, India's merchandise exports surged a record 38.91 per cent on-year to $37.81 billion and imports too rose a record 38.55 per cent to $59.48 billion. India's textile export exports are growing after a decade-long stagnation, textile exports during April-December 2021 touched $29.8 billion, compared to as compared to $21.2 billion in the same period last year. It was up 31 per cent year-on-year. All these developments show that things are moving in the right direction.
But are we ready for such long term growth in the garment export business? A major challenge is going for long term growth is labour shortage. I wish to draw attention to this major issue which will have impact on more than any issue. It had shocked the industry two years ago and even now there is apprehension of the same. The issue was the return of migratory workers from established hubs/ metro cities to their villages. In 2020, lockdown was imposed and months after that factories struggled for months to arrange workers again. Though the Government's move of lockdown was not properly planned and at the same time, there was no support from the factories, few allied factors were also responsible for this issue. Now, this year so far we have not seen lockdown and various Governments are comparatively well prepared. But the major point is that nothing has improved on the garment manufacturing front which is majorly based on these migratory workers of states like Uttar Pradesh, Bihar, Odisha, Jharkhand.
Established garment manufacturing hubs across India Delhi-NCR, Bangalore, Tirupur, Ludhiana, Kolkata, Ahmedabad and Jaipur, etc., are totally helpless without these migratory workers. But what significant industry has done for its workers? Nothing. Good working conditions, salary/wage following law of the land, is something that basic rights of workers and factories have to do this as they are bound for the same by the law. Overseas buyers motivate/forced the garment exporters to support workers with a variety of training sessions that help them little in their technical work as well as their life upliftment.
What else do workers need and factories can do, especially for migratory workers? The answer is simple and also known to garment manufacturers. Workers need a reasonably good dormitory/ housing facilities/hostel depending upon they are living alone in established hubs or their family is also with them.
It is not just a pandemic that create a shortage of workers, despite the full effort for skill development, garment manufacturing industry more or less always has a shortage of skilled and good workers. More than a decade ago, to overcome the issue of labour shortage and to reduce dependency on migratory workers, big garment manufacturers started factories in remote areas where the labour was easily available.
Majority of big and medium level garment factories are still operating in established hubs from where they have started and will expand only in nearby areas. So labour shortage will be continue be a challenge. So to overcome this challenge best and permanent solution can be ensuring to have housing for workers.
Some of the companies and majorly in South India are successfully offering this facility to a large chunk of their workers so others can also go for this. Yes, it has its own cost, is not easy to manage, have some risk also. But at the same time, it has a lot of benefits also. Workers will be able to save more money and time if they are provided residence facilities near factories. And factories will have less absenteeism, less worker turnover ratio, more loyal workers, and good image as well. As far as cost factor is concerned, stakeholders like factories, workers, Government and NGOs can have collaborative efforts for this.
After all Government is promoting housing by various ways be it PM Awas Yojana, the incentive for affordable housing. Workers are also paying rent no matter they are living together in groups in satisfactory rooms or even slum-type areas. Medium and large size companies do have a legal obligation under Corporate Social Responsibility (CSR). Even if any change at policy level is required to execute housing for workers, it should not be a major challenge as such housing will create a win-win situation for all. For example, Noida (Uttar Pradesh) have thousands of unsold flats and under-construction buildings which can be used to live with little improvement/finishing.
Garment manufacturers especially exporters have logic that their business is seasonal and they don't have a full business for 12 months. So they don't need to buy or invest hugely in housing plans, such flats can be taken on rent. State Governments can also give some subsidies for such initiatives. Even as of now garment manufacturers have a cost of buses and fuel to arrange transportation for their workers. Once they have the intention, the cost of housing or managing the same will not be a massive challenge. Trade bodies, the local associations have to play a proactive role to make this happen. The majority of workers also need to change their mindset as they have to be more disciplined when they are using good facilities and saving a good amount of money.
Global conditions are somehow in India's favour and this is high time to take care of its workers and their core issues. Otherwise, there are enough chances that India will have good business, state of the art plants, and 'costly' raw materials, but without full and motivated workforce there will be a struggle to complete these orders.
(The author owns a garment manufacturing setup in a rural area, which employs mostly women workers)