India’s Battery Storage Push
Why Smart Energy Storage is Key to Clean Power and E-Mobility
India’s Battery Storage Push
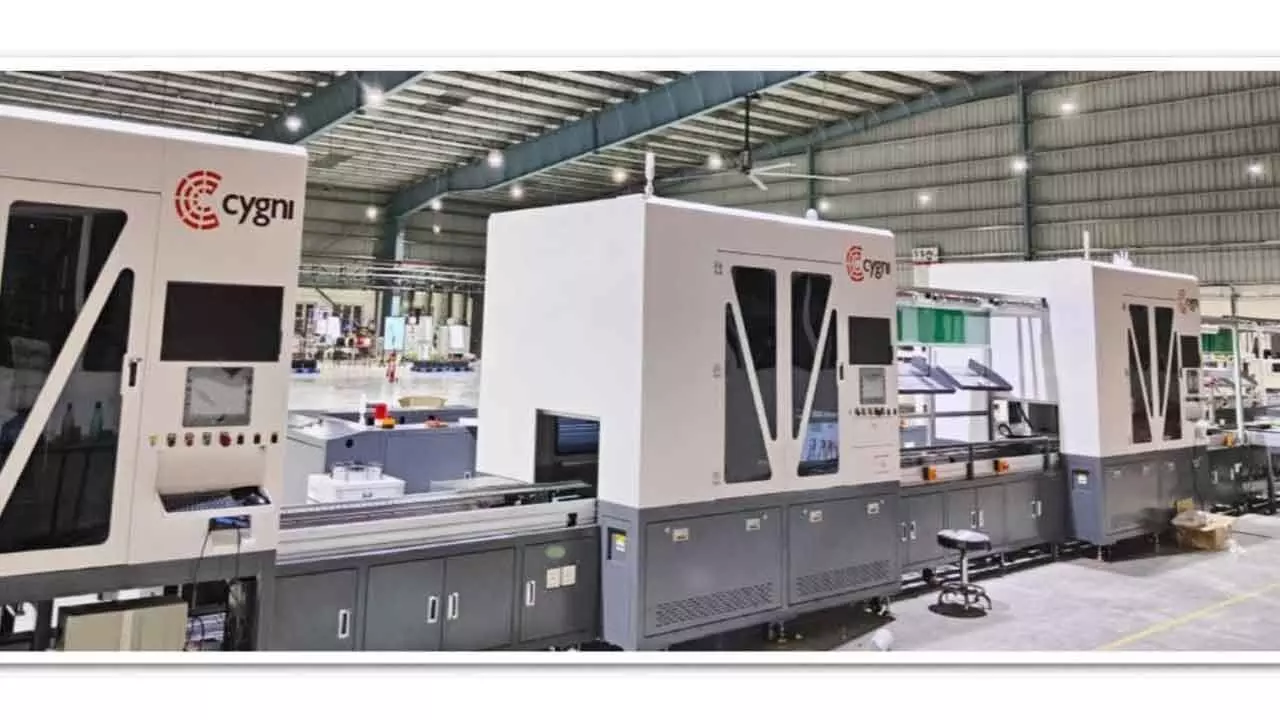
The next decade will be pivotal for India’s battery storage industry. With a growing tender pipeline, rising EV adoption, and mounting grid integration challenges, energy storage is no longer an ancillary technology — it is foundational. For stakeholders across manufacturing, utilities, finance, and policy, the message is clear: investing in battery storage capacity, technology, and infrastructure is essential to realize India’s clean energy, mobility, and Net Zero goals
India stands at a defining juncture in its energy journey. While electric mobility, renewable energy, and grid modernization advance rapidly, a silent but critical gap has emerged: the country’s ability to store energy effectively and at scale. From powering millions of electric vehicles to balancing renewable-rich grids, battery energy storage systems (BESS) will shape the reliability, adaptability, and sustainability of India’s future energy landscape.
The numbers lay bare the urgency and opportunity. According to the Central Electricity Authority (CEA, 2023), India will require at least 41.7 GW / 208 GWh of battery energy storage systems (BESS) and 18.9 GW of pumped hydro storage (PSP) by 2030. Fast-forward to 2032, and the India Energy Storage Alliance (IESA) projects a total market size of 250 GWh of BESS capacity — a staggering leap from the 0.36 GWh operational as of January 2025.
Further, as of Apr 2025, a robust pipeline of 114 GWh of energy storage system (ESS) tenders has been announced — spanning 77 projects. This includes 70 GWh of PHS and 44 GWh of BESS, with storage projects now accounting for 23% of total tendered capacity. Clearly, this is no longer a niche segment — battery storage is central to India’s clean energy and mobility ambitions.
Electric Vehicles: The
First Wave of Demand
Electric vehicles (EVs), particularly two-wheelers and three-wheelers, have emerged as the primary catalysts for battery adoption in India. With over 10 million EVs expected to ply Indian roads in the next 3–5 years, the demand for advanced battery packs — ranging from 1.5 kWh to 10 kWh — is accelerating sharply.
Unlike Western markets that emphasize large-format batteries for electric cars (4Ws), India’s focus on smaller vehicles and last-mile delivery unlocks unique battery design and application opportunities. India’s diverse geography and usage patterns demand smart, adaptable, and safe battery packs — a challenge where technology will be the differentiator.
Battery-swapping ecosystems, particularly for commercial and delivery operators, are poised for significant expansion. Yet, challenges around standardization and interoperability remain. The upcoming battery-swapping standards from the Indian government are expected to unlock new avenues in this space.
Beyond vehicles, stationary applications — including telecom towers, data centres, residential complexes, and commercial buildings — are emerging as significant demand drivers for energy storage. With India’s ambitious renewable energy targets and the increasing need to balance grid variability, large-scale BESS solutions are moving from pilot projects to mainstream deployment.
A spate of recent tenders (44 GWh BESS) signals strong institutional interest in leveraging battery storage for grid support, frequency regulation, and peak shaving. Independent Power Producers (IPPs) and utilities are also actively exploring grid-scale stationary storage projects, often in hybrid configurations with solar or wind energy.
Bridging Supply Gap
Currently, India imports most of its battery cells from China, Korea, Japan, and Taiwan. However, nearly all balance-of-system components — battery management systems, enclosures, bus bars, wire harnesses — are increasingly manufactured locally. The next logical leap is cell manufacturing localization, expected to take shape within the next 5 years, supported by government ACC-PLI incentives and industry collaborations.
Several private players have commissioned gigafactories focused on EV and stationary storage battery packs — including a recently operational , Phase 1 of 4.8 GWh facility in Hyderabad’s E-Mobility Valley, capable of producing 46,000 battery modules of 105kWh annually. Such facilities, equipped with Automated BESS Assembly Line, with automated cell sorting, laser welding, cell characterization and End-of-Line (EOL) testing, is engineered for advanced, high-quality BESS module manufacturing, leveraging globally recognised best practices such as Poka-Yoke-enabled stations and end to end traceability are crucial stepping stones toward domestic self-reliance.
“The intersection of India’s software strength and manufacturing scale offers a unique opportunity to create intelligent, IoT-enabled battery packs that ensure safety, performance, and longevity.” The next decade will be pivotal for India’s battery storage industry. With a growing tender pipeline, rising EV adoption, and mounting grid integration challenges, energy storage is no longer an ancillary technology — it is foundational. For stakeholders across manufacturing, utilities, finance, and policy, the message is clear: investing in battery storage capacity, technology, and infrastructure is essential to realize India’s clean energy, mobility, and Net Zero goals.
The Moment Is Now
Author Bio: Mr Venkat Rajaraman is the Founder/CEO at Cygni Energy and an Advisory Committee member of National Centre for Photovoltaic Research and Education (NCPRE), India. Cygni, a leading storage technology company with cutting-edge expertise in Energy Storage Systems (Telecom, Commercial & Industrial storage and large scale energy storage etc). Cygni has deployed over 200MWh of storage solutions and powered over 150,000 EVs. Cygni’s currently has a fully automated battery manufacturing facility at Hyderabad. Cygni’s new Greenfield project is currently operational which supports a capacity of 4,800MWh.