Centre finalises green hydrogen mission scheme
Hydrogen hub scheme ready to be rolled out, pilot projects being undertaken in steel, shipping, and road transport sectors
image for illustrative purpose
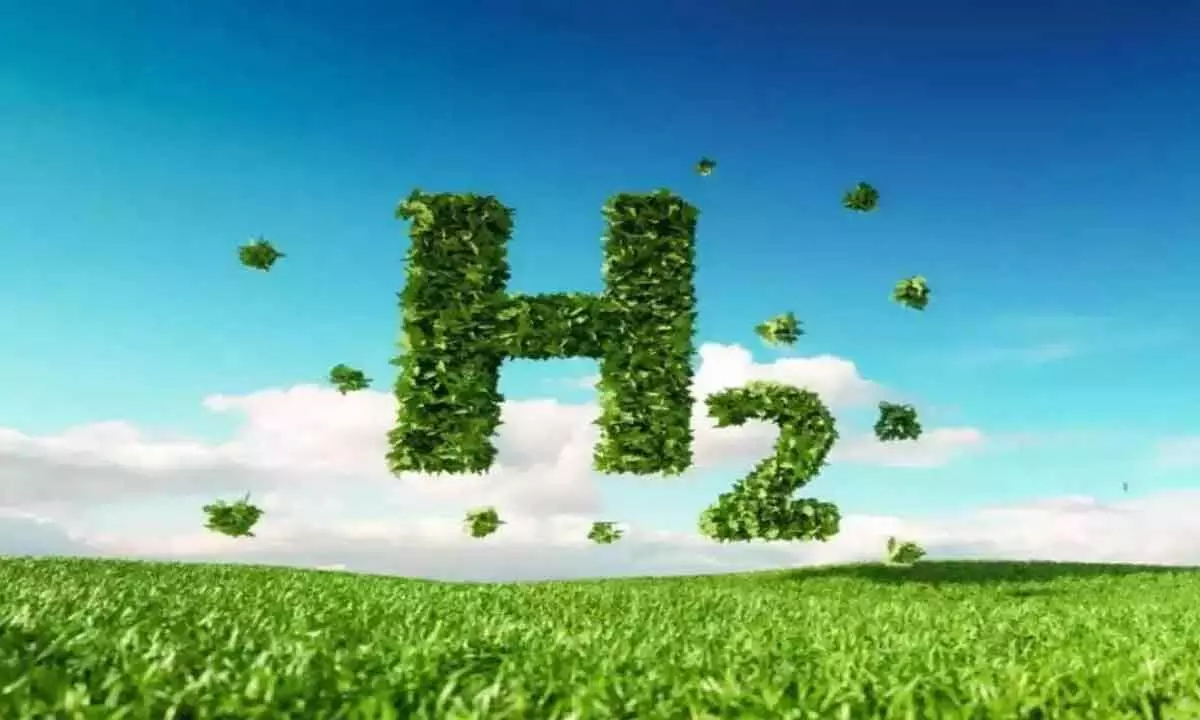
Towards Cleaner Fuel
- MNRE allocates Rs 400 cr to boost Green Hydrogen Mission
- Govt keen on stipulating standards for Type IV hydrogen cylinders
- Type IV cylinders lightest and most suitable for vehicle applications
New Delhi: All schemes under the National Green Hydrogen Mission have been finalised and that the scheme for hydrogen hubs is ready to be rolled out. Pilot projects are being undertaken in steel, shipping, and road transport sectors, official sources told Bizz Buzz. The Ministry of New & Renewable Energy (MNRE) recently announced the allocation of Rs 400 crore for research and development to boost the National Green Hydrogen Mission. It is intended to provide guidance for developing a vibrant R&D ecosystem which can help commercialize green hydrogen and contribute to India’s ambitious climate and energy goals.
The central government is also keen on the stipulation of standards for Type IV cylinders for storing hydrogen. At present, India has standards for Type III cylinders, whereas all over the world Type IV cylinders are prevalent.
According to the Science Direct website, hydrogen storage vessels can be classified into four standard types: Type I, Type II, Type III, and Type IV. Type I is an all-metal vessel (usually steel) and hence the heaviest, typically employed in industry for stationary use. It can store hydrogen only at the pressure of 200-300 bar.
Type II is a metal liner hoop-wrapped composite cylinder, weighing less than Type I cylinder. However, both Types I and II vessels are unsuitable for vehicle applications due to their low hydrogen storage density, arising from their heavyweights, and also because of hydrogen embrittlement challenges.
Type III vessels comprise a fully wrapped composite cylinder with a metal liner that serves as the hydrogen permeation barrier. The metal liner is made of aluminum, which solves the problem of embrittlement and it contributes more than 5 per cent to the mechanical resistance. They are reliable at pressures up to 450 bar. Type IV vessels comprise a fully wrapped composite cylinder with a plastic liner (typically high-density polyethylene), which acts solely as the hydrogen permeation barrier. Type IV vessels are the lightest of the pressure vessels, making them most suitable for vehicle applications, and they can endure high pressures up to 1,000 bar.