The Critical Role of Technology in 3PL Warehouse Businesses
image for illustrative purpose
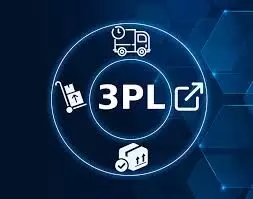
In today's fast-moving logistics industry, Third-Party Logistics (3PL) warehouse businesses are under constant pressure to perform faster, more accurately, and at a lower cost. With rising customer expectations, global supply chains, and multi-channel retailing, traditional manual methods are no longer sufficient. This is where modern technology steps in, transforming warehouse operations and creating new opportunities for growth and efficiency. For 3PL business owners looking to keep up, leveraging the right tools—such as an easy to use warehouse software—has become essential to stay competitive and deliver exceptional service.
The need for real-time visibility, seamless integration, and data-driven decision-making continues to grow. Whether you’re running a single facility or managing multiple warehouses for different clients, adopting the right warehouse management system (WMS) can significantly streamline operations. If you're considering a system upgrade or evaluating your current setup, see here for warehouse software options tailored specifically for 3PL environments.
The Modern Demands of 3PL Warehousing
3PL providers handle complex logistics for various clients, including inventory storage, pick-and-pack services, labeling, shipping, and returns management. With the boom in e-commerce, businesses now expect real-time inventory updates, fast order fulfillment, and flawless accuracy. This shift in demand has made traditional, manual systems inadequate for today’s high-volume, high-velocity logistics operations.
Why Technology Is Critical in 3PL Operations
1. Enhancing Operational Efficiency
Technology automates key warehouse processes such as inventory control, order picking, and shipment tracking. Automation not only reduces errors but also dramatically improves processing time and workforce productivity. For example, barcode scanning and automated stock adjustments help eliminate miscounts and ensure that stock levels are always accurate.
Using cloud-based WMS, warehouse staff can access real-time data from mobile devices, reducing paperwork and enabling instant communication between teams. These small improvements compound into major operational savings.
2. Providing Real-Time Visibility and Transparency
3PL clients expect to see exactly where their goods are, how much stock is available, and when their orders are being processed. A modern WMS provides real-time dashboards, shipment tracking, and automated alerts, giving clients and operators peace of mind.
Through technology, 3PLs can offer a level of transparency that builds trust and strengthens client relationships. When clients can track their inventory and orders 24/7, it reduces support inquiries and improves satisfaction.
3. Scalability for Business Growth
One of the biggest challenges in warehousing is scaling operations without compromising service quality. A robust WMS enables 3PL businesses to expand by handling higher volumes and new clients without needing to redesign internal processes.
Cloud-based systems are particularly effective for this, offering flexible pricing, remote access, and easy setup for new users or locations. Whether you’re opening a new warehouse or onboarding a large client, scalable software ensures that your infrastructure can support the growth.
4. Driving Smart, Data-Backed Decisions
Good technology doesn’t just process data—it turns it into actionable insights. A WMS can track productivity metrics, error rates, inventory turnover, and client performance. These insights help business owners make informed decisions about staffing, warehouse layout, and client profitability.
For instance, by analyzing pick times and order accuracy, you can pinpoint where inefficiencies occur and adjust workflows accordingly. Over time, this data-driven approach creates a more agile, responsive operation.
5. Enabling Client Integration and Custom Services
Modern 3PL clients often use their own systems—like Shopify, WooCommerce, or ERPs—to manage orders. Warehouse software must integrate seamlessly with these platforms to automate data exchange and reduce manual entry.
With proper integrations, 3PL providers can also offer tailored services such as branded packaging, returns processing, and same-day shipping. These value-added offerings differentiate your services and increase client loyalty.
What 3PL Business Owners Must Ensure with Technology
While implementing technology brings many benefits, the right choices must be made to avoid costly mistakes. Here are several factors every 3PL business owner should consider when adopting warehouse technology:
1. Ease of Use
Technology should simplify, not complicate. Choose an easy to use warehouse software that your team can quickly learn and operate with minimal training. Systems with intuitive dashboards, mobile functionality, and drag-and-drop interfaces help reduce onboarding time and errors.
Warehouse staff are often more focused on physical tasks than digital ones—so software usability is critical for long-term success.
2. Cloud Accessibility and Flexibility
Today’s 3PL operations need the freedom to manage warehouses remotely. A cloud-based WMS gives owners and managers real-time access from any location, improves data security, and simplifies updates. It also supports remote teams, multi-location syncing, and business continuity during disruptions.
3. Robust Features and Automation
Your software should support the full lifecycle of 3PL operations, including:
Multi-client inventory tracking
Order and returns management
Automatic billing and invoicing
Integration with e-commerce and courier platforms
Customizable reports and KPIs
The more features that can be automated, the fewer errors and delays your team will face during daily operations.
4. Data Security and Compliance
With more data flowing through cloud systems, protecting client and customer data is critical. Ensure your software provider complies with local data regulations (such as GDPR) and offers encryption, backups, and user-based permissions. A breach in warehouse data can have serious financial and reputational consequences.
5. Support and Training Resources
Look for a vendor that offers comprehensive support, including onboarding assistance, online resources, and a dedicated support team. A responsive support system ensures smooth implementation and minimizes operational downtime in case of issues.
6. Scalability and Continuous Updates
The right WMS should evolve with your business. Make sure the software is regularly updated, offers new features based on customer feedback, and adapts to emerging industry trends like AI-based forecasting or robotics integration.
Conclusion
In a competitive logistics market, technology isn’t just a support function—it’s the heart of a successful 3PL warehouse business. From automating operations and improving accuracy to providing real-time insights and enhancing client satisfaction, the benefits of warehouse technology are extensive and game-changing.
Business owners who invest in an easy to use warehouse software set their operations up for greater flexibility, cost savings, and long-term scalability. Whether you’re upgrading your current system or exploring new tools, be sure to prioritize usability, integration capabilities, security, and customer support.
To get started with a solution that’s built specifically for 3PL businesses, see here for warehouse software options that combine ease of use with powerful logistics features.