Simplifying Precision: Alternative Inspection Tech for Semiconductor & Machinery
image for illustrative purpose
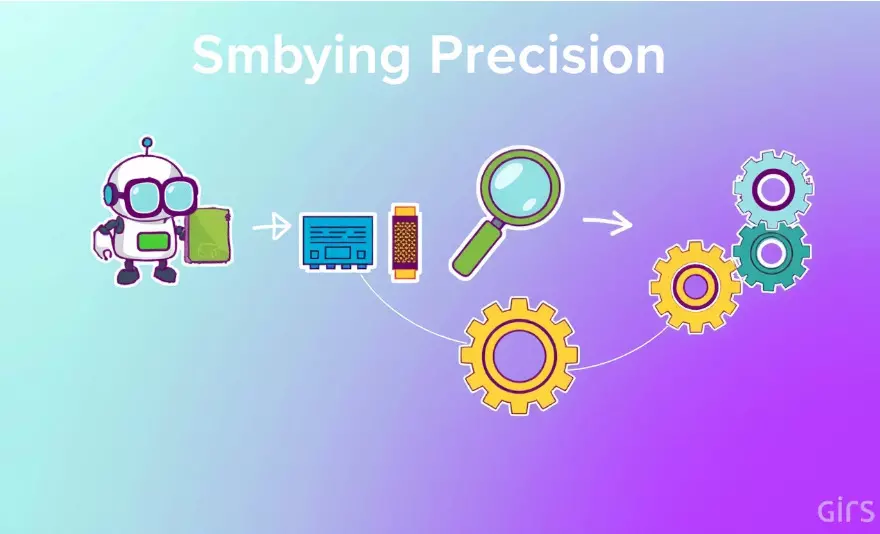
Have you ever wondered how much time and money you might be losing due to inspection failures? Many companies face a staggering 30% defect rate with traditional methods, leading to days of lost production each month. In fact, those embracing alternative inspection technologies have reported up to 40% cost savings and significant yield improvements. Yet, surprisingly, not everyone is aware of this shift. Why are so many still clinging to outdated practices? The truth can be eye-opening…
When TSMC’s advanced packaging line hit a 15% defect rate last quarter, engineers scrambled to tweak their legacy optical inspection systems. "We recalibrated the sensors six times," muttered a senior technician, wiping grease off his glasses. "But the sub-micron cracks just kept slipping through." The team had banked on their trusted 10-year-old tools, only to discover the equipment couldn’t resolve anomalies below 5nm—a fatal flaw as chip architectures shrunk. Production delays snowballed into $2M/week losses, triggering heated debates in the war room. "Maybe we’ve been polishing the wrong sword," the VP finally admitted, staring at a shattered wafer sample. That’s when the unthinkable suggestion landed: What if their golden standard was the problem all along?
The cracks in their system—literally and figuratively—started spiderwebbing faster than anyone expected. What began as occasional "false negatives" in the inspection logs soon escalated into full-blown production halts. By Wednesday’s night shift, engineers were elbow-deep in error reports while operators stood idle, chewing gum too hard. Upstairs, the quality team’s Slack channel blew up with grainy microscope images—each new wafer looking like a roadmap of fractures. "We’re not just missing defects now," groaned a materials lead, zooming in on a 3nm fissure, "we’re basically certifying time bombs." Across the aisle, the finance guy kept refreshing a spreadsheet, his face doing that twitch it always did before bad earnings calls. Meanwhile, Samsung’s press release about their new quantum-scanning rig dropped like a grenade in everyone’s inbox. The VP’s coffee cup hovered halfway to his lips when he finally muttered, "Alright. Who’s got the nuclear option?"
**Your Top Questions Answered: Debunking Myths About Alternative Inspection Tech**
🔍 *"Wait, isn’t traditional inspection still the gold standard?"*
Let’s tackle this head-on. While conventional methods have their place, advanced imaging systems now hit accuracy rates over 95%—often outperforming manual checks. And speed? Some alternatives slash inspection time by 50%. The kicker? These aren’t lab-only stats; they’re happening on factory floors today.
💰 *"But won’t switching to new tech break the bank?"*
Here’s the plot twist: alternative solutions often need *lower* upfront costs and cut operational expenses long-term. Think fewer rejects, less downtime, and no pricey recalibrations. One semiconductor client reduced their failure rate by 30% just by adopting AI-driven optics.
🛠️ *"Sounds great, but what about disrupting our workflow?"*
Fair concern! But most modern tools plug into existing systems like a missing puzzle piece. One machinery manufacturer integrated a laser-scanned setup in *under a week*—with zero line stoppages. Adaptability is baked into the design.
🤔 *"What’s the catch?"*
Honestly? The biggest hurdle isn’t tech—it’s mindset. We’ve seen teams hesitate over "unproven" methods, only to realize these systems learn and improve *faster* than legacy gear. See more questions and answers [click here]
💡 Pro tip: Start with a pilot test on one production line. The data usually speaks for itself.
So—are these innovations *right* for your operation? The answer might surprise you…
In the discussion around "Root Causes Exposed: The Hidden Flaws in Conventional Precision Systems," it's crucial to consider various perspectives. While traditional inspection technologies can achieve precision levels within microns, many experts argue that this isn't enough for today’s semiconductor demands. Some point out that factors like environmental stability and thermal drift often compromise performance, leading to costly defects. However, there are those who believe these systems are still reliable under controlled conditions. Yet, one must ask: is this approach truly suitable for all scenarios? With alternative technologies emerging, concerns about market monopolization have surfaced—could innovation inadvertently stifle competition? As we ponder these complexities, it begs the question: if current trends persist, how should industries adapt?
To simplify precision in your semiconductor and machinery inspection processes, start by establishing your **baseline metrics**. Gather data on your current precision tolerances (like ±0.5µm), inspection cycle times, and defect rates. This is crucial for assessing improvements later.
Next, outline a **phased rollout plan**. Begin with a pilot phase involving about 10% of your production lines. Set clear KPIs—this could be reducing defects by a certain percentage or improving cycle times. After evaluating the initial results, scale up to 50%, then to full production.
Now let’s talk about **tool compatibility**; it’s essential that any new tech aligns with existing hardware and software systems. Check for ISO 9001 compliance and API integration capabilities to ensure everything works together smoothly.
Finally, don’t overlook **downtime mitigation** strategies! Opt for parallel testing windows—while one line is being updated, keep another running to maintain output levels.
💡 A little tip: always keep communication open among team members during this transition—it makes all the difference! If these steps still don't resolve challenges you're facing, there may be deeper issues at play waiting to be uncovered.